Understanding the Role of a China Plastic Injection Molding Manufacturer
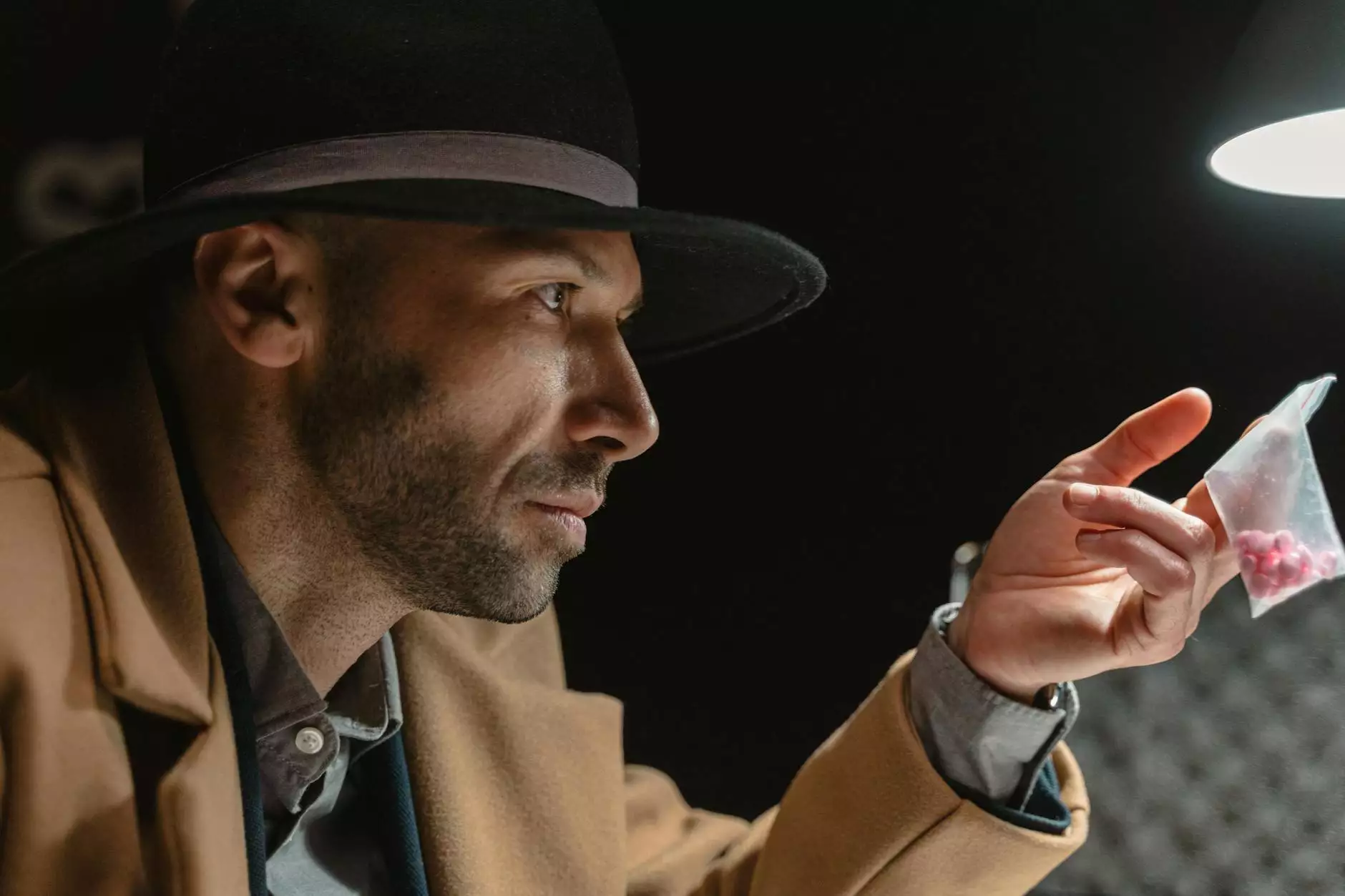
The manufacturing landscape has evolved considerably in the past few decades, with China plastic injection molding manufacturers leading the charge in terms of innovation, efficiency, and cost-effectiveness. The process of plastic injection molding is a cornerstone in a wide array of industries, from automotive to consumer goods, providing manufacturers with a reliable and scalable method to produce high-quality plastic parts with precision. In this article, we will delve deep into the intricacies of plastic injection molding, the advantages of working with manufacturers, and how this industry is shaping the future of manufacturing.
The Basics of Plastic Injection Molding
Plastic injection molding is a manufacturing process where plastic is heated until it becomes fluid-like, then injected into a mold. Once the material cools, it solidifies into the desired shape. This process is not only efficient but also allows for intricate designs which are essential in modern product manufacturing.
- Material Versatility: Plastic injection molding can utilize a variety of polymers, allowing manufacturers to choose materials best suited for their applications.
- Precision Production: Advanced machinery ensures that each piece is produced to precise specifications with minimal variance.
- High Volume Output: Once a mold is created, thousands of identical components can be produced, making it cost-effective for large production runs.
Advantages of Partnering with a China Plastic Injection Molding Manufacturer
Choosing to work with a China plastic injection molding manufacturer offers numerous benefits. Here are some of the key advantages:
1. Cost Efficiency
One of the primary reasons businesses turn to Chinese manufacturers is significant cost savings. Labor and material costs in China are lower, allowing for reduced production costs. This economic advantage enables companies to offer competitive pricing in their markets.
2. High-Quality Standards
Many of the leading China plastic injection molding manufacturers adhere to international quality standards, ensuring that the products you receive are of high quality. Manufacturers often employ advanced quality control systems and technologies to maintain consistency and quality in their production.
3. Innovation and Technology
Chinese manufacturers are at the forefront of using the latest technologies in plastic injection molding, including 3D printing, CNC machining, and advanced molding techniques. This allows for rapid prototyping and improved design capabilities, making it easier to innovate and adapt products to market demands.
4. Extensive Industry Knowledge
With years of experience in the global manufacturing industry, companies like Deep Mould possess extensive knowledge about the needs of various sectors. Their expertise can guide your selection of materials and machinery, leading to optimized production processes tailored for your specific needs.
5. Scalability
As your business grows, so too can your production capabilities. A reliable China plastic injection molding manufacturer can help you scale your operations quickly, adjusting production volumes according to your requirements without compromising on quality.
The Manufacturing Process Explained
Understanding the steps involved in plastic injection molding can help you appreciate the complexity and capabilities of this process:
- Material Selection: The first step is choosing the right material for your project. Factors such as strength, flexibility, and thermal properties play a significant role in this decision.
- Creating the Mold: Once the material is selected, a mold is designed and manufactured. This is a crucial step as the design will ultimately dictate the product's shape and features.
- Melting the Material: The selected plastic is then heated until it becomes molten, ready for injection.
- Injection: The molten plastic is injected into the mold under high pressure, filling every detail of the design.
- Cooling: The material cools and solidifies within the mold, taking on its final shape.
- Demolding: Once cooled, the mold is opened, and the finished product is ejected.
- Finishing: After demolding, additional processes may be required, such as trimming and surface finishing, to ensure the product meets specifications.
Choosing the Right Manufacturer
When selecting a China plastic injection molding manufacturer, it is critical to consider various factors to ensure you partner with a reliable and competent provider:
1. Experience and Reputation
Research the manufacturer’s experience in the industry. Look for client reviews, testimonials, and case studies. An established company with a strong reputation is more likely to deliver quality service and products.
2. Capabilities
Evaluate their engineering and design capabilities. A manufacturer should offer comprehensive support, including designing, prototyping, and mass production. Check if they can handle complex designs and large-scale production.
3. Quality Control Measures
Inquire about their quality assurance processes. Effective quality control measures ensure that every product matches your required specifications. Look for manufacturers with certifications like ISO 9001.
4. Communication
Good communication is essential for a successful partnership. Ensure that the manufacturer can communicate clearly in your preferred language and is responsive to inquiries.
5. Post-Production Support
Consider the level of post-production support offered. This can include assistance with packaging, logistics, and after-sales service, all of which are vital for your product’s success.
Emerging Trends in Plastic Injection Molding
The world of plastic injection molding is constantly evolving. Here are some notable trends that are shaping the future of this industry:
1. Sustainability Efforts
With increasing environmental concerns, manufacturers are focusing on sustainability. This includes using recycled materials in production as well as implementing more eco-friendly manufacturing processes.
2. Advanced Automation and AI
Automation and artificial intelligence are being integrated into the manufacturing processes, leading to improved efficiency and reduced human error. Smart machines can optimize production processes in real-time, providing significant advantages.
3. Customization and On-Demand Production
As consumer demands shift towards personalized products, the ability to customize designs is becoming more important. Many manufacturers are adapting to offer on-demand production capabilities to accommodate this trend.
4. Industry 4.0 Integration
The rise of Industry 4.0 has encouraged manufacturers to incorporate smart technologies, including IoT and big data analytics, into their systems. This integration allows for enhanced monitoring, predictive maintenance, and overall efficiency improvements.
Conclusion
In conclusion, working with a China plastic injection molding manufacturer provides numerous benefits, including cost savings, high-quality production, and access to advanced technologies and expertise. As the manufacturing landscape continues to transform through automation, sustainability, and customization, businesses need to partner with innovative manufacturers who can meet their evolving demands.
Exploring the potentials of plastic injection molding is essential for any business looking to optimize its production processes and maintain competitive advantages in today's fast-paced market. As leaders in the industry, manufacturers like Deep Mould are at the forefront of these developments, paving the way for future advancements in manufacturing solutions.